Consulting
We listen to and understand the needs of each customer in order to propose the best solution.
Twenty years of experience acquired by Espo in the field of polyurethane technology is at the full service for our customers to accompany and support them in every stage of the work, from the feasibility analysis of the design procedure up to its completion.
Thanks to the continuous collaboration with the customer, the high quality of the products used, the professionalism of our team and the constant monitoring of the production processes, Espo ranks among the leading companies in the production of polyurethane products.
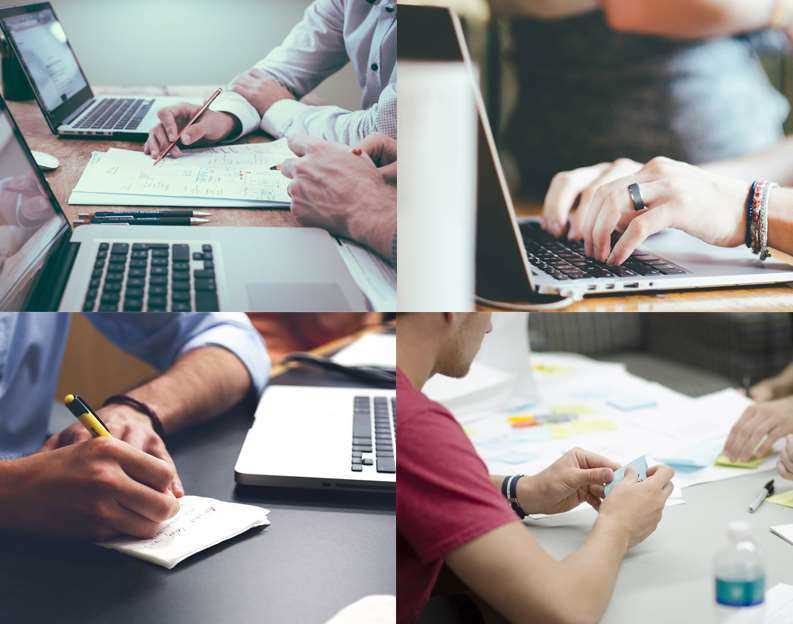
Model
design
The ideas begin to take shape through a scale prototype of the final product.
Through careful preliminary analysis, the most appropriate type of polyurethane will be selected and adequate assistance will be provided for the definition of the geometric figure. All depending on the end use of the product.
The techniques that we usually use for the realisation of the models are:
- Hand carving carried out by skilled craftsmen
- 5-axis pantograph processing
- 3D printing for rapid prototyping
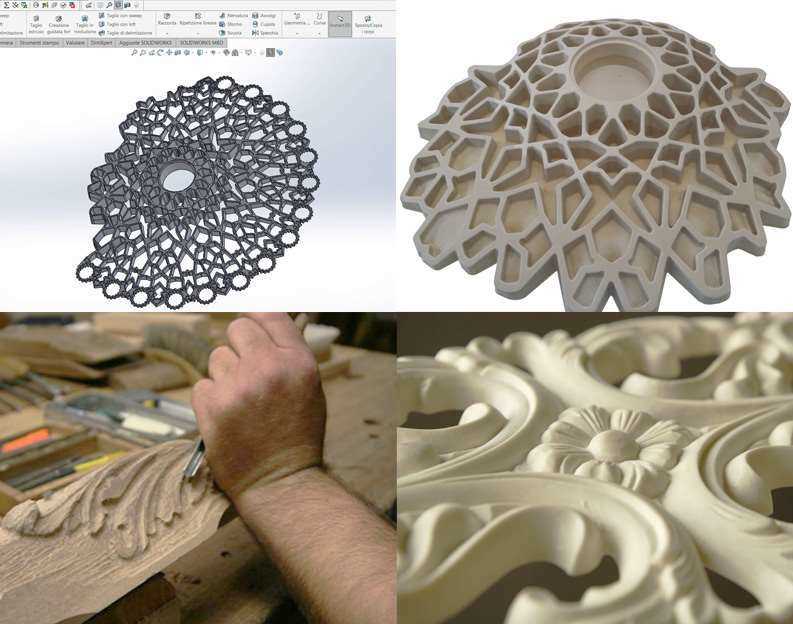
Mould
realization
Care, dedication and perfection to ensure an excellent unbeatable product
The impeccability of the finished product depends on the perfection of the mould. For this reason, the quality of the mould must be the primary prerogative when starting the realisation of the product.
The moulds are made of epoxy resin or aluminium.
Epoxy resin moulds are the best compromise between cost and production capacity, the low initial investment makes them the most versatile and the most widely used for the production of items in polyurethane.
All moulds are thermostatically controlled to ensure perfect and constant repeatability of the artefact.
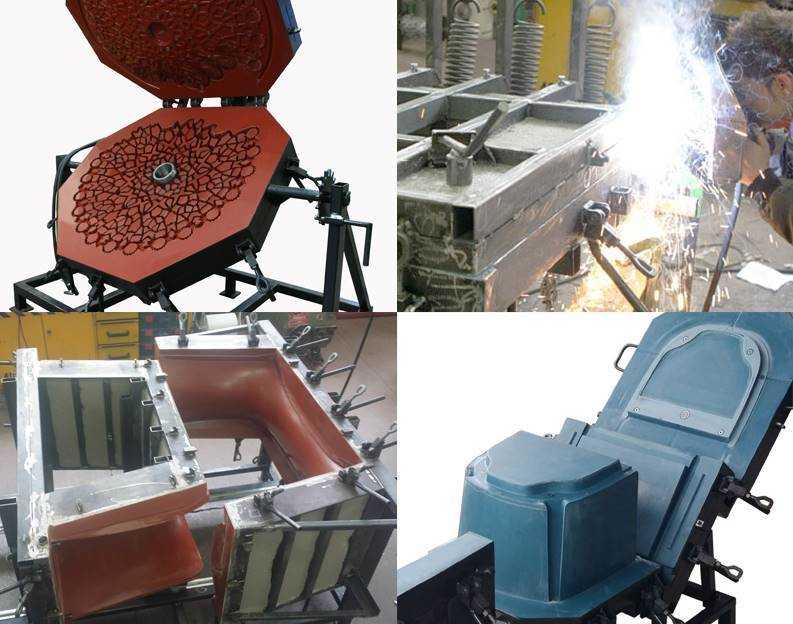
Moulding
The heart of our company, where ideas and projects take shape
Polyurethane is a polymer formed by the union of two chemical substances: Polyol and Isocyanate.
These two components are combined and blended by a specific foam dispensing machine. The resulting chemical reaction in the first place makes the material expand and immediately after solidifies it.
The heart of the production is made up of 7 low and high pressure foaming plants where the moulding of different types of polyurethane is carried out.
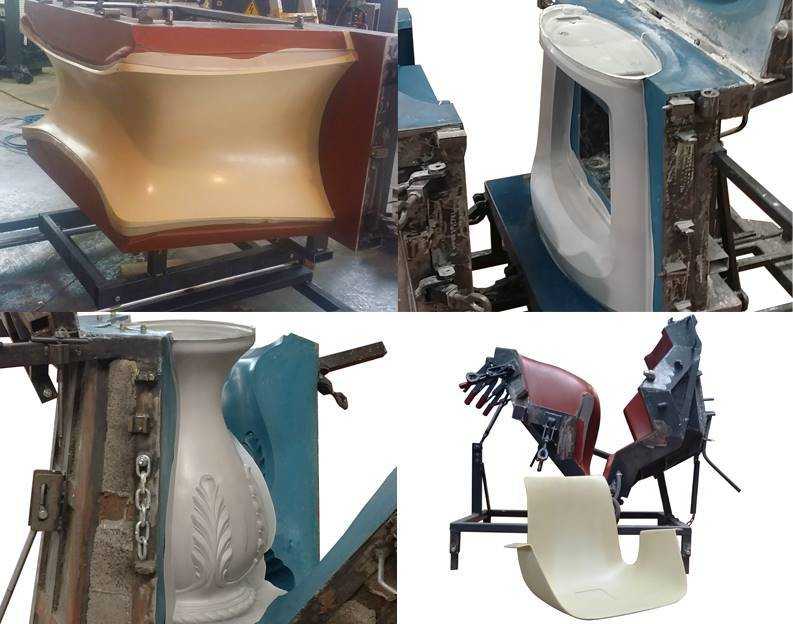
Finishing
Attention to detail and uniqueness of the product thanks to the touch of the craftsman.
From the moulding we pass on to the finishing stage, where the products are finished, milled, shaped and sanded. The internal construction of the shapes guarantees the result of the assembly stage.
And it is at this precise moment that the touch of the craftsman can confer uniqueness and singularity to the artefact.
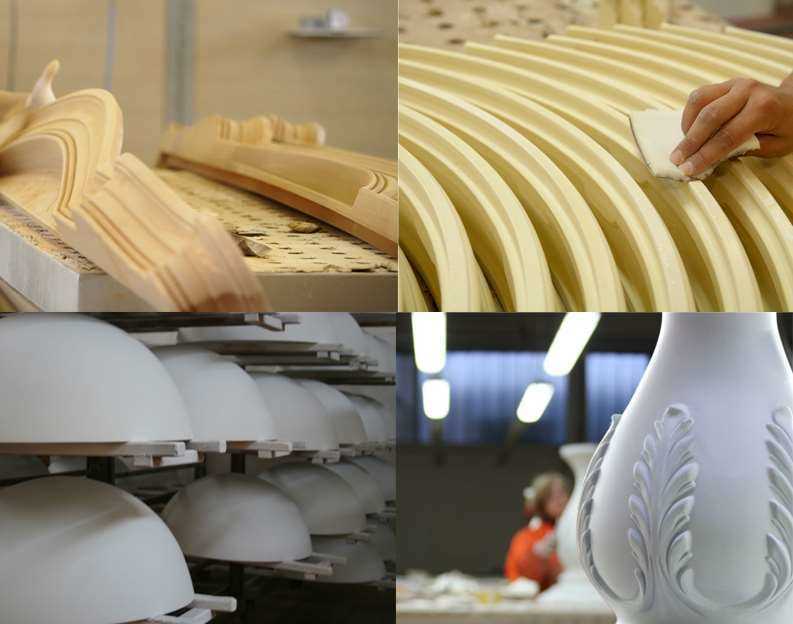
Painting
The pride of our production is the painting department.
The process is managed entirely within the company over an area of 2000 square meters and consists of a primer system and pressurised cabins for the finishing touches.
Twenty years of experience and a meticulous eye for detail allow us to obtain excellent results approved by the most important names in furnishing and design.
The continuous search for new effects and new finishes allows us to push the implementation of polyurethane products to the extreme.
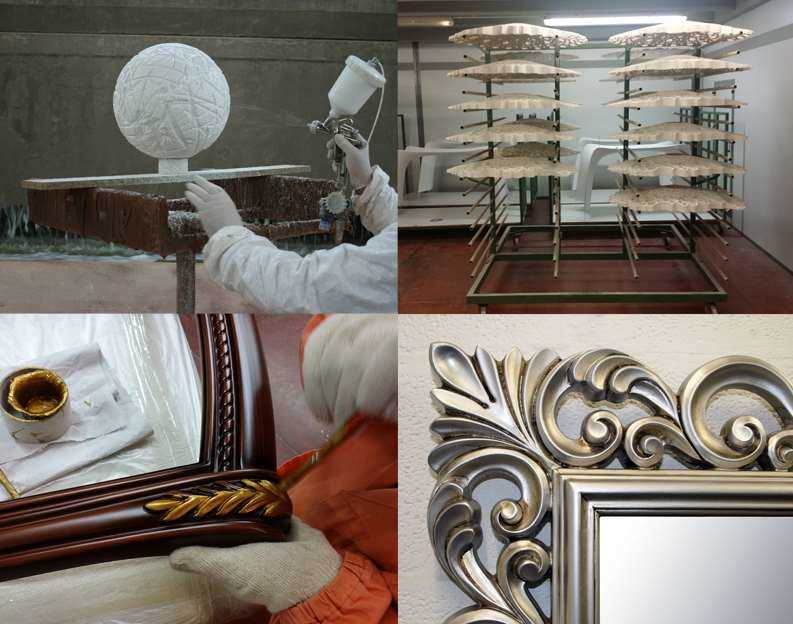
Packaging
Preservation of the integrity of the product through the use of ad hoc packaging.
The care and attention applied during all the stages of the realisation of the final product also continue in the packaging stage. After a careful quality control to make sure that all the parameters have been met and that the customer's requirements have been fulfilled, we move on to choose the most appropriate packing.
This stage is essential to keep the artefact intact during transport.
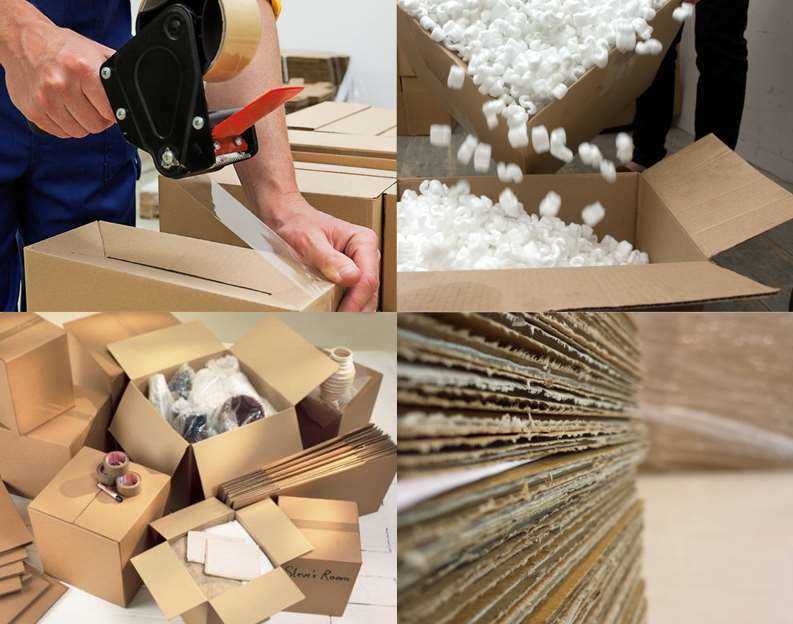